While I have made a lot of tiles, tile commissions are another level of stress and commitment entirely. The fixed dimensions of a room and the changing nature of clay through its making and firing process require a mastery of the materials and process that can feel a bit daunting
So when a friend and long time client approached me with a commission for a tile piece for her screened porch I was a bit hesitant. However, my plans to buy a house required ready cash so I agreed after some negotiation.
Initially she was thinking of a floor mosaic, which was a lot of my hesitation, not feeling confident that I could produce a glazed tile that wouldn’t be super slippery when its wet. once we switched to a surround of the floor, I felt I could begin.
The first step was planning and designing. Working out the square footage and then calculating the shrinkage of the tiles is a super difficult proposition, especially since I make my own clay and can’t really do better than estimate shrinkage rates since batches are only about 150 lbs at a time and shrinkage changes from batch to batch.
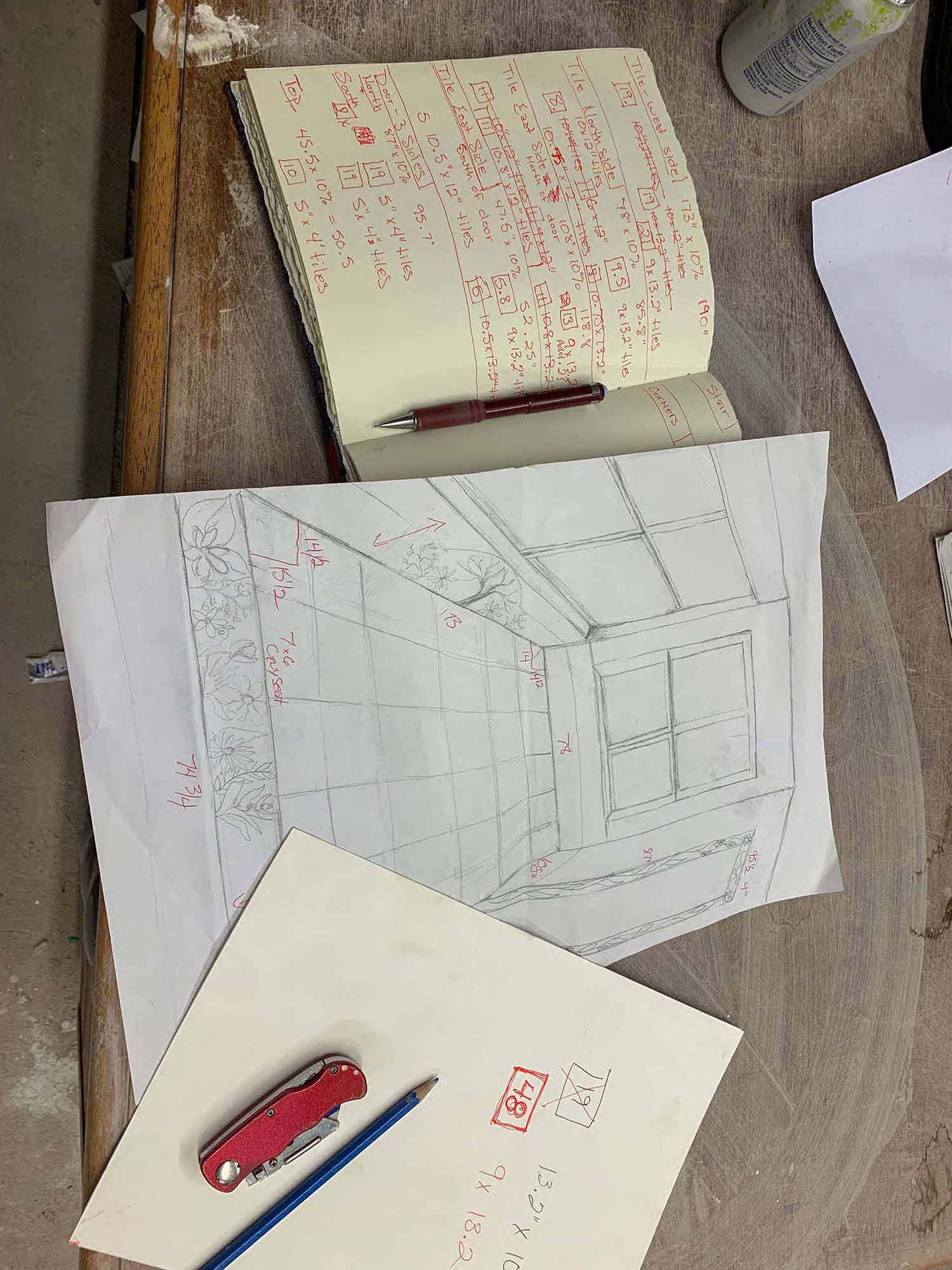
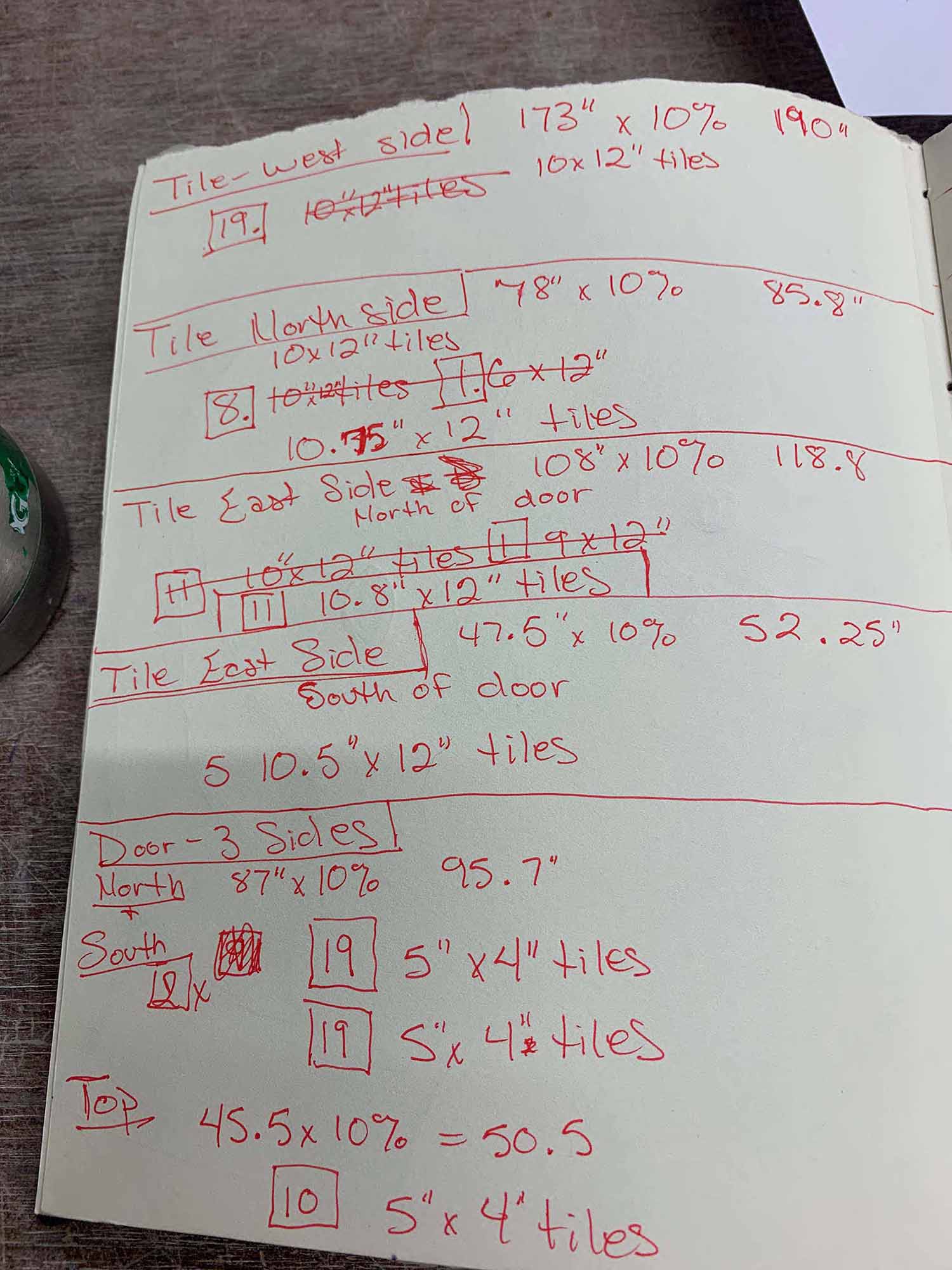
This step is of course critical to making a bid on the job for the client. Having all the problems and expectations on the table from the beginning is vital for everyone involved.
From there, my next step was to begin testing my making and glazing ideas.
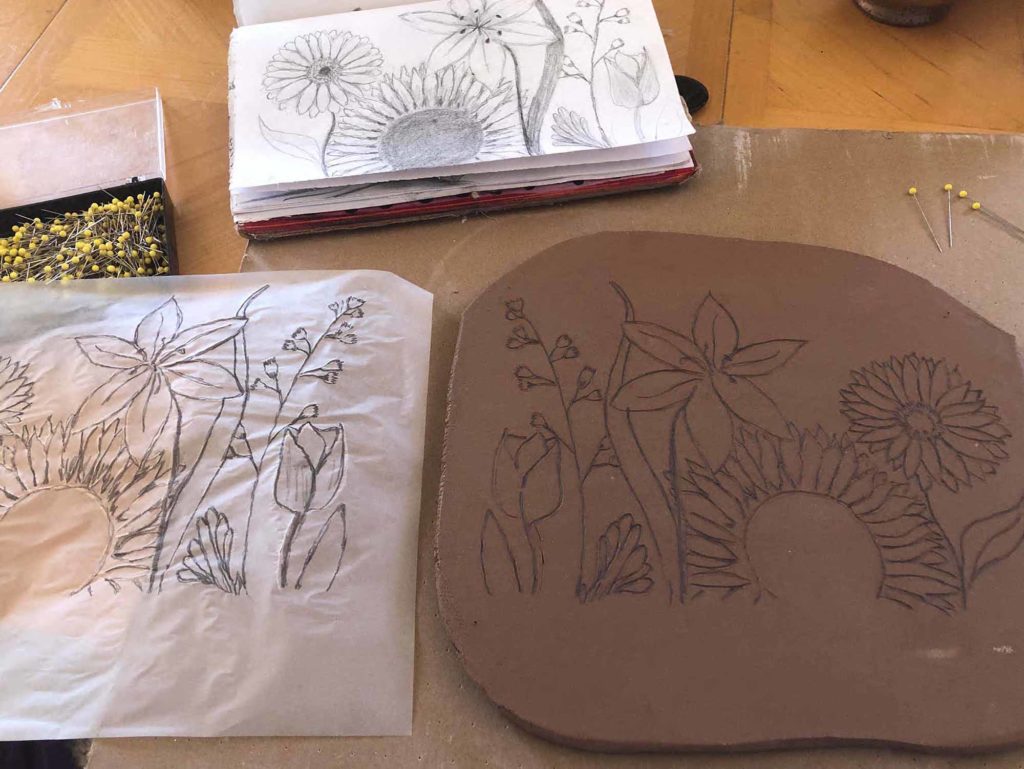
Once the design and glaze choices were approved I started generating the tiles in earnest. This first half of the project, detail and intricacy were important, so I spent a lot of time looking at flowers
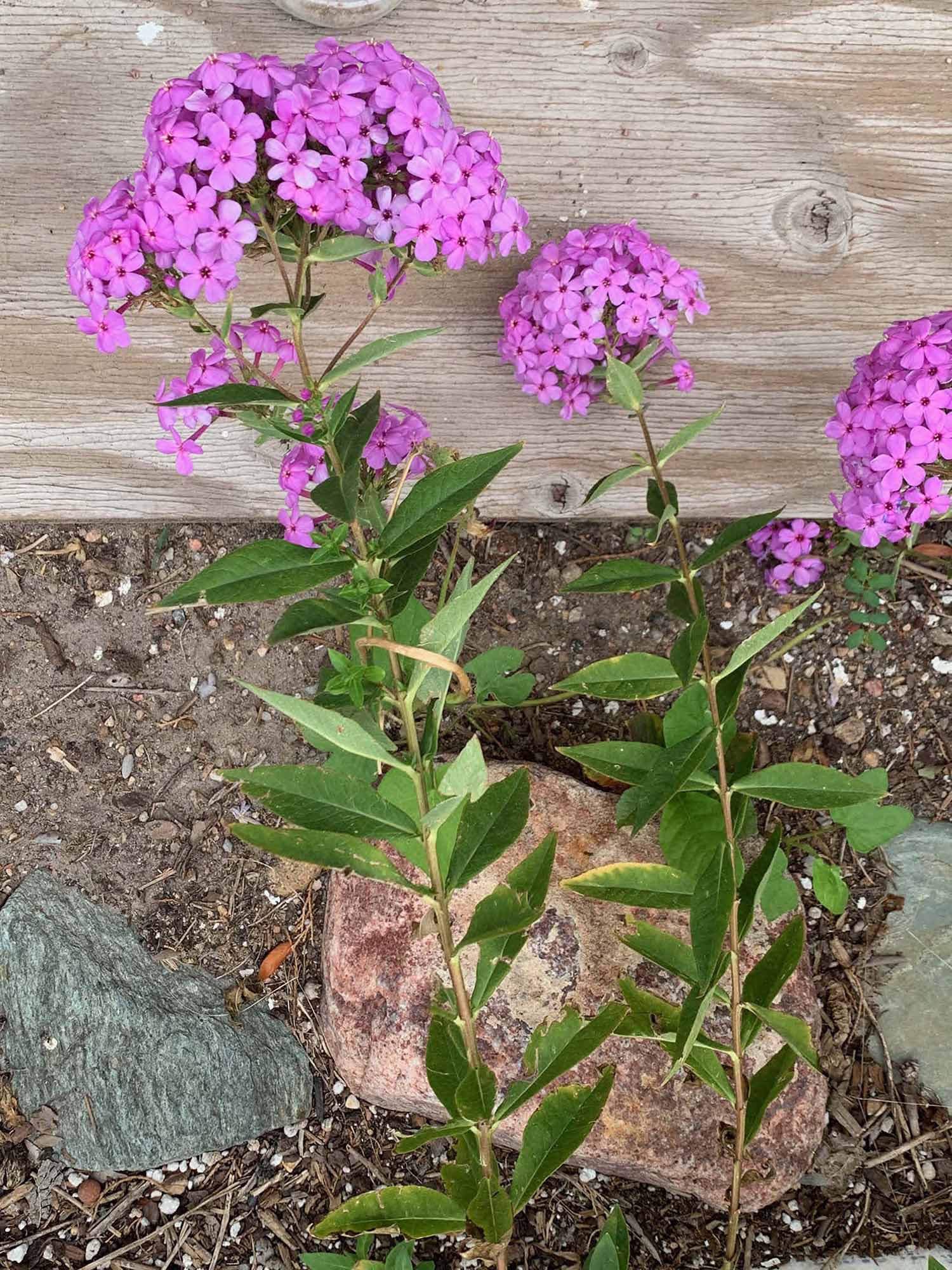
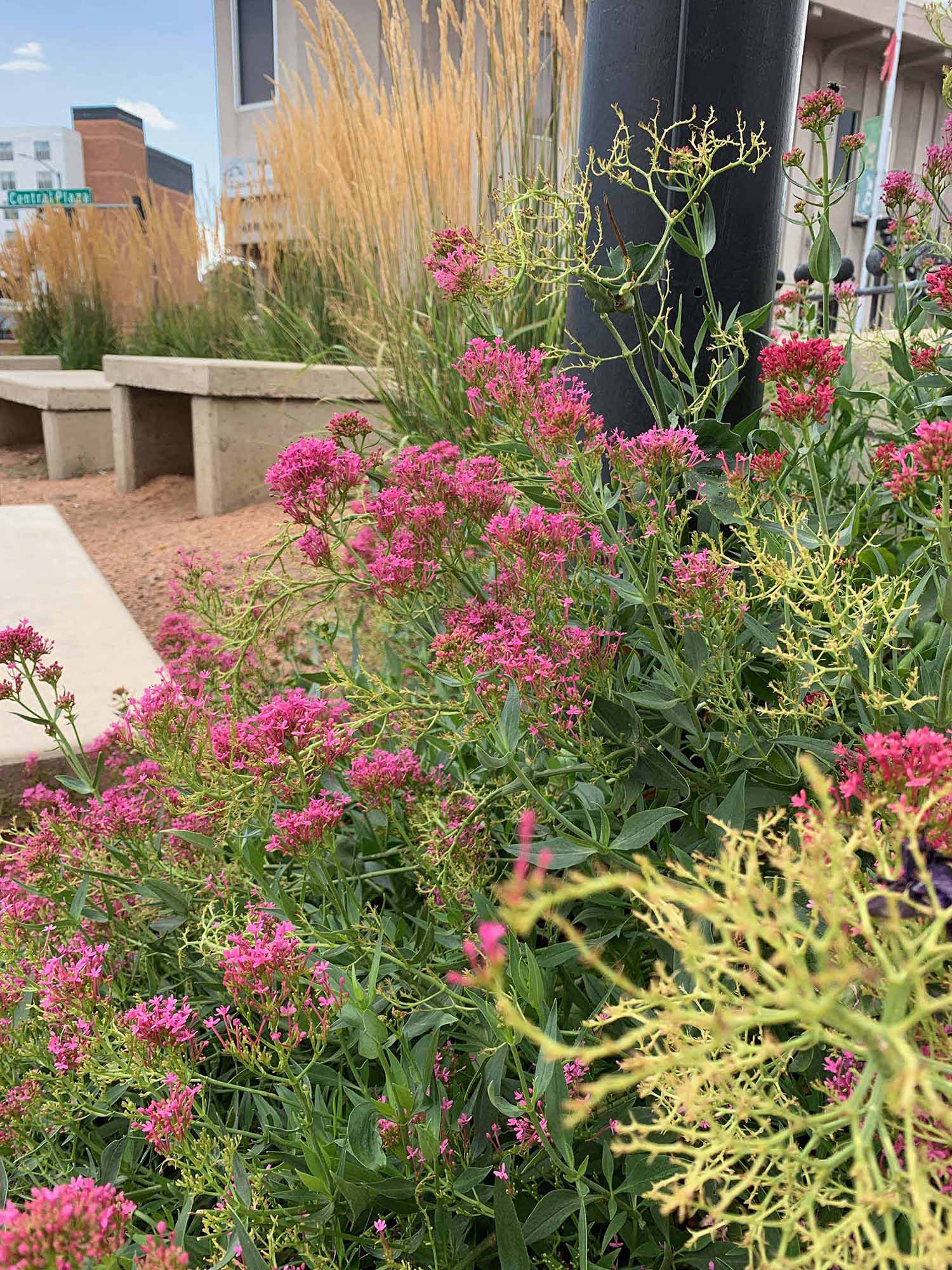
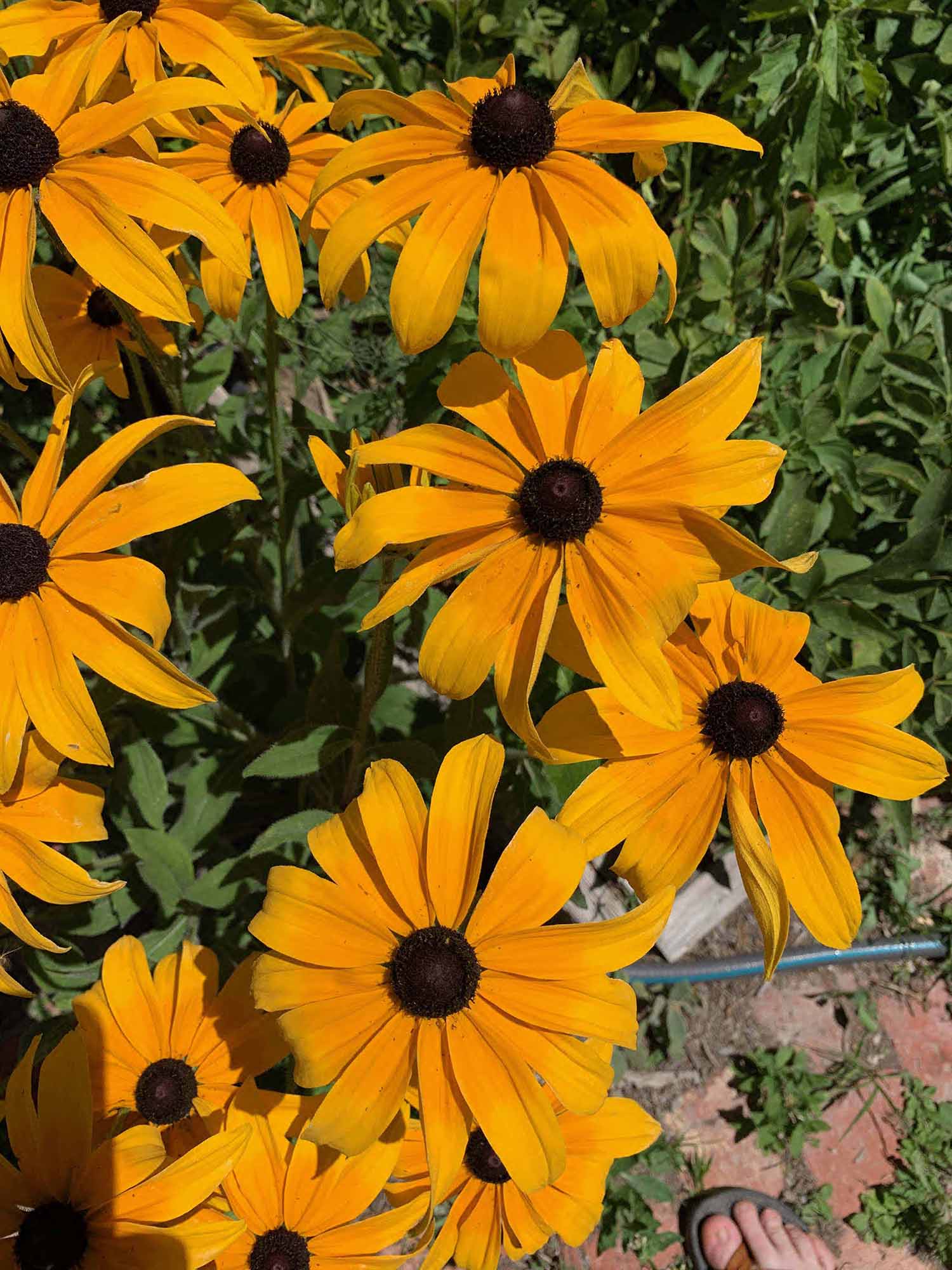
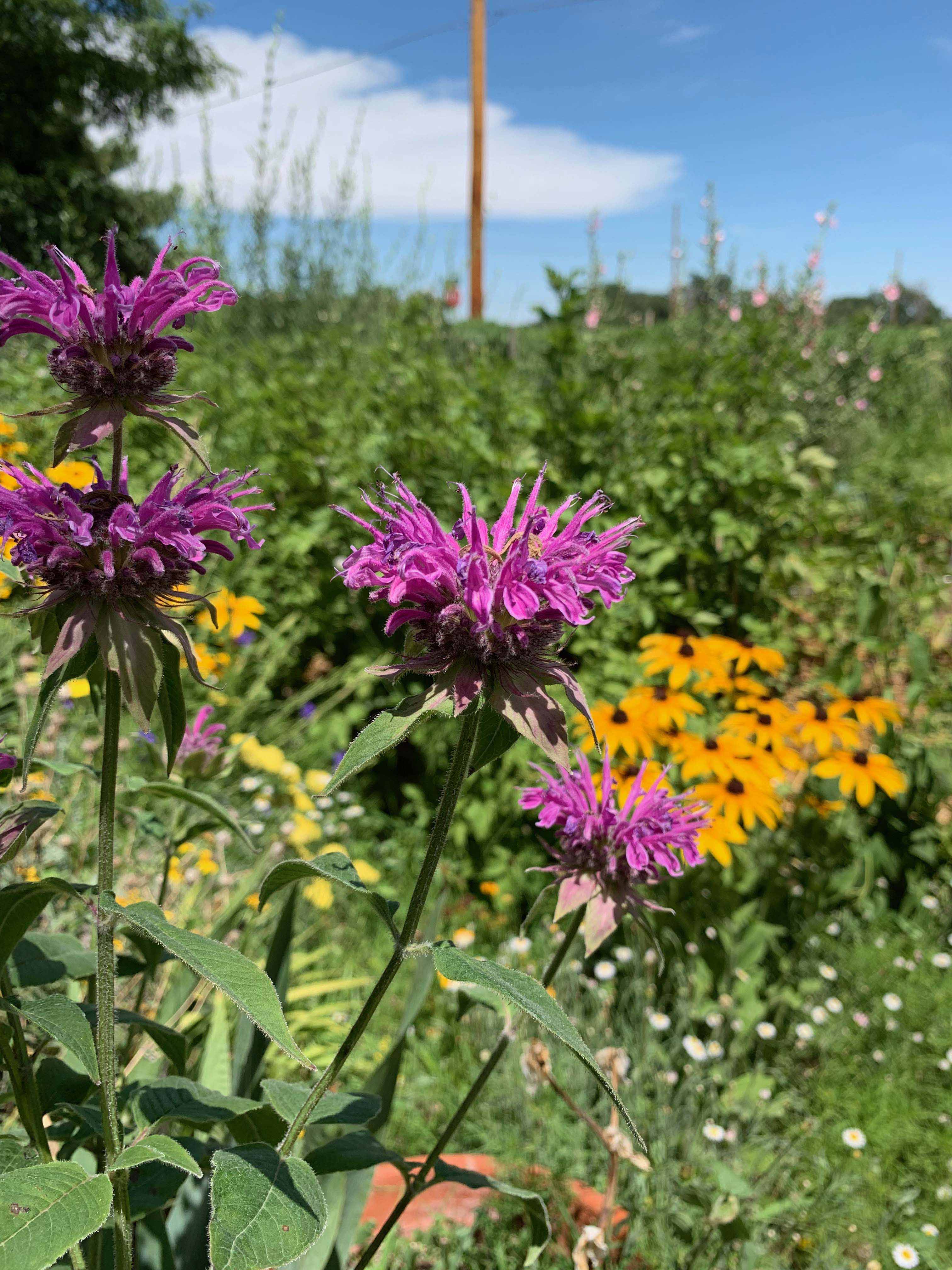
Once the research phase ended I switched focus to the studio. First the tiles must be made. As I mentioned above shrinkage is a major consideration, one way to deal with this is to make all the tiles at the same moisture content in the slab. This means cutting them as soon as they are made, which makes them impossible to move for some time. Once made, preventing the tiles from warping becomes a central concern. You might notice that the tiles in this group have a lot less detail at this stage, the earlier tiles had quite a bit more detail, some of which actually made the warping problem worse. The great thing about a job this size is the opportunity to learn along the way. You also might notice fewer number of designs, I had the client choose 5 of her favorites from the first batch to further simplify the process. part of this was the cost of my time, I badly underestimated my costs on this job and had to do what I could to make it more feasible for my studio. Also some of the process was just wasted time. The mishima clay layers were completely lost in the iron wash process after the first firing
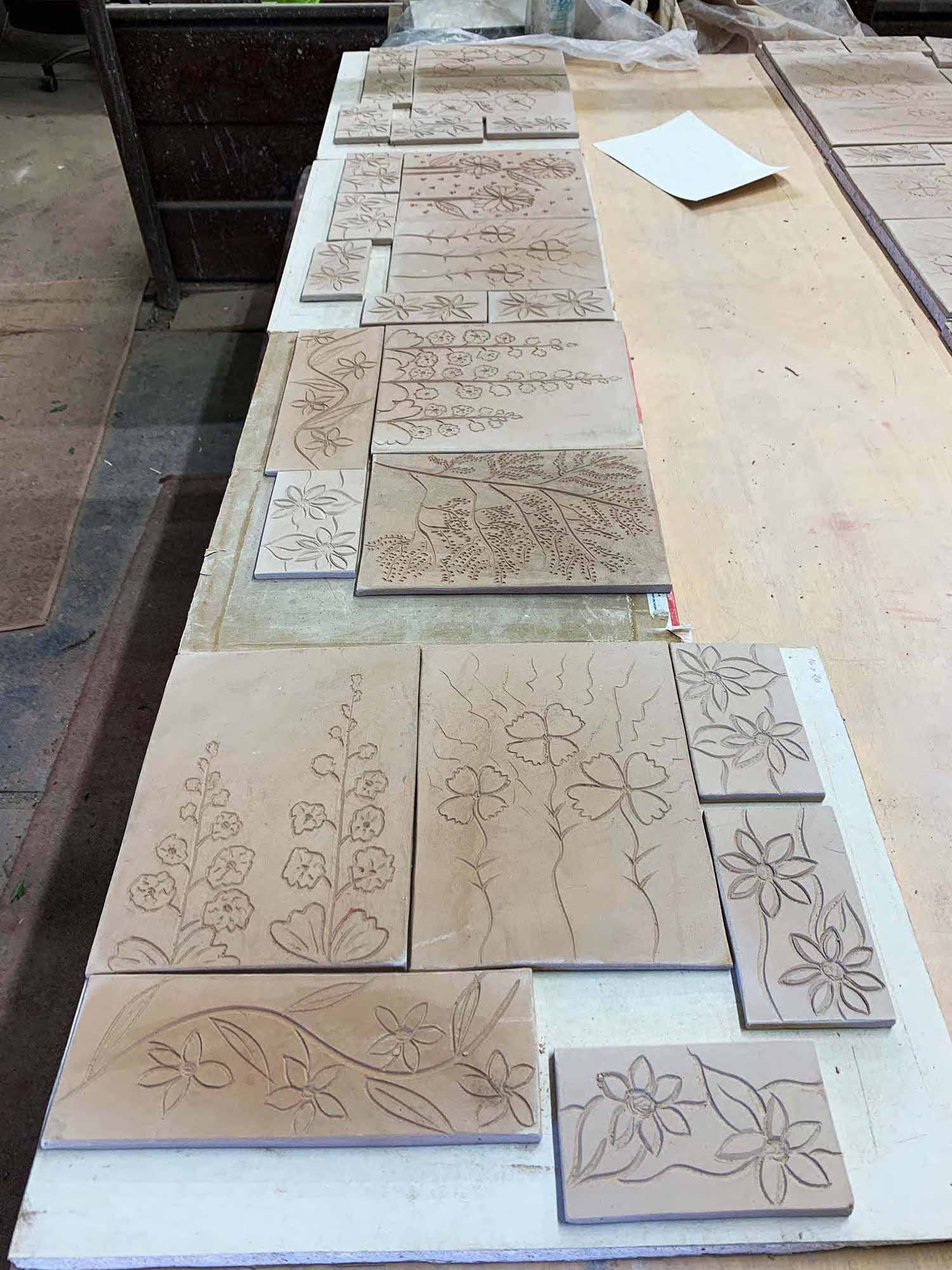
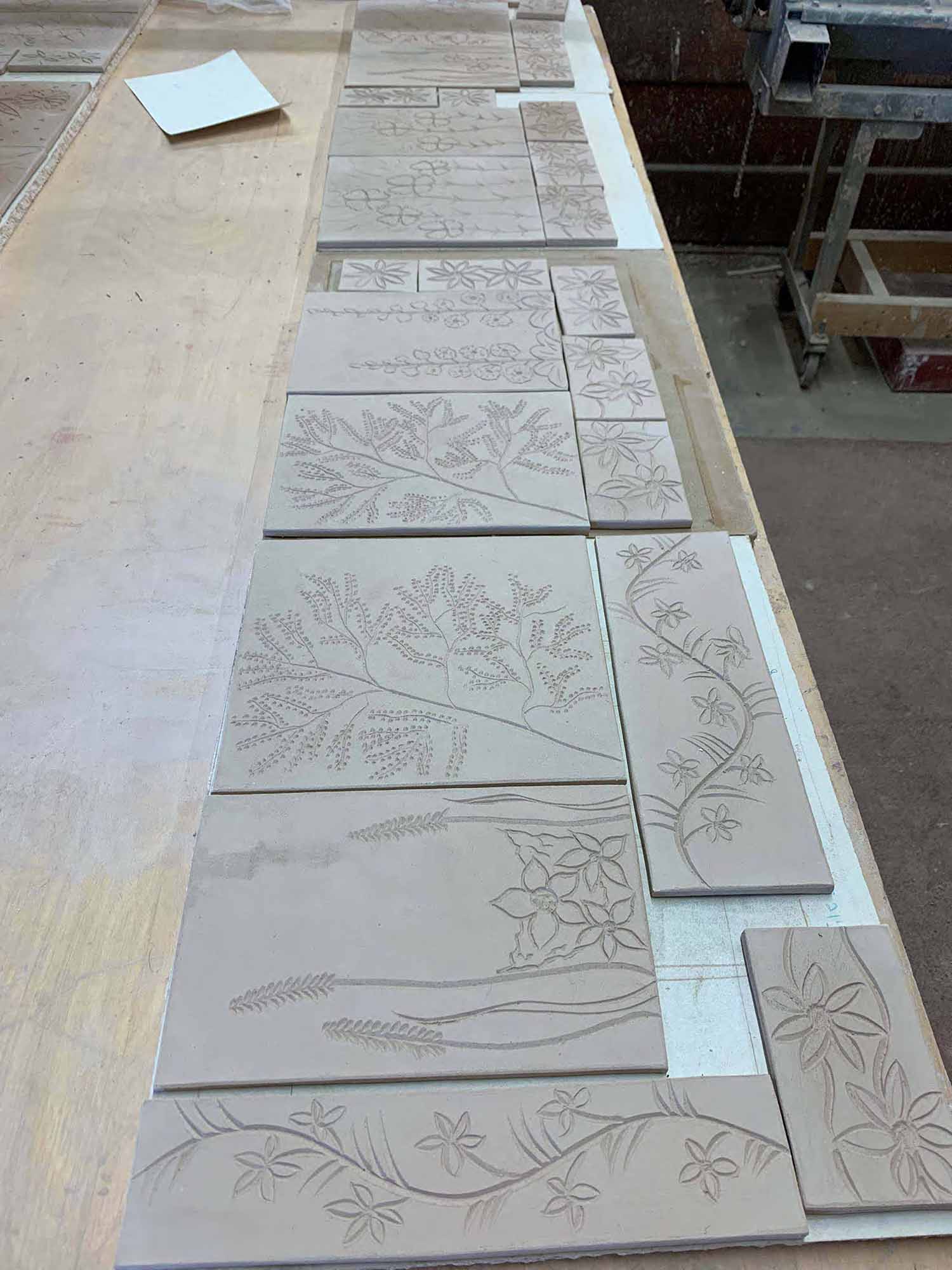
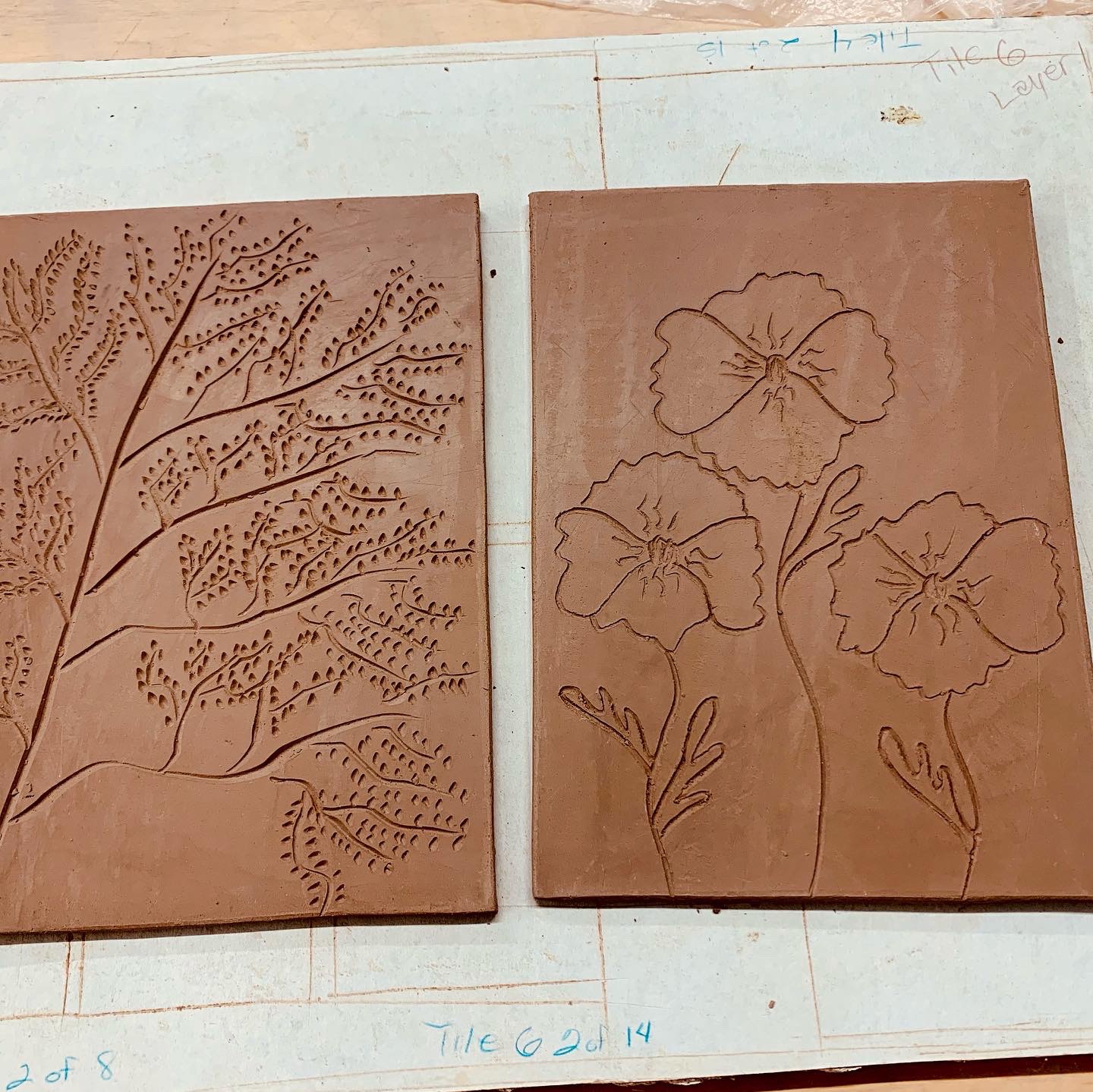
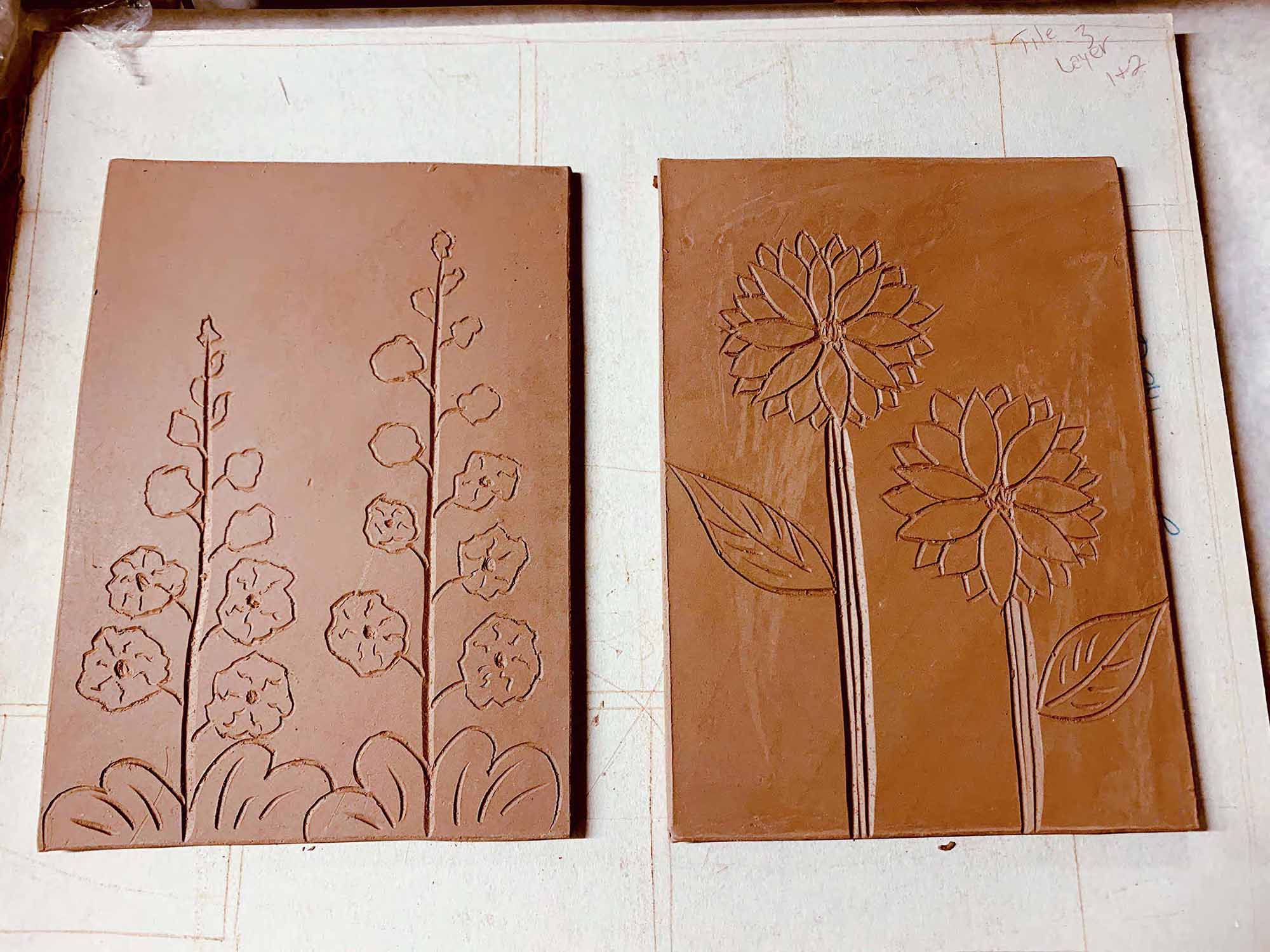
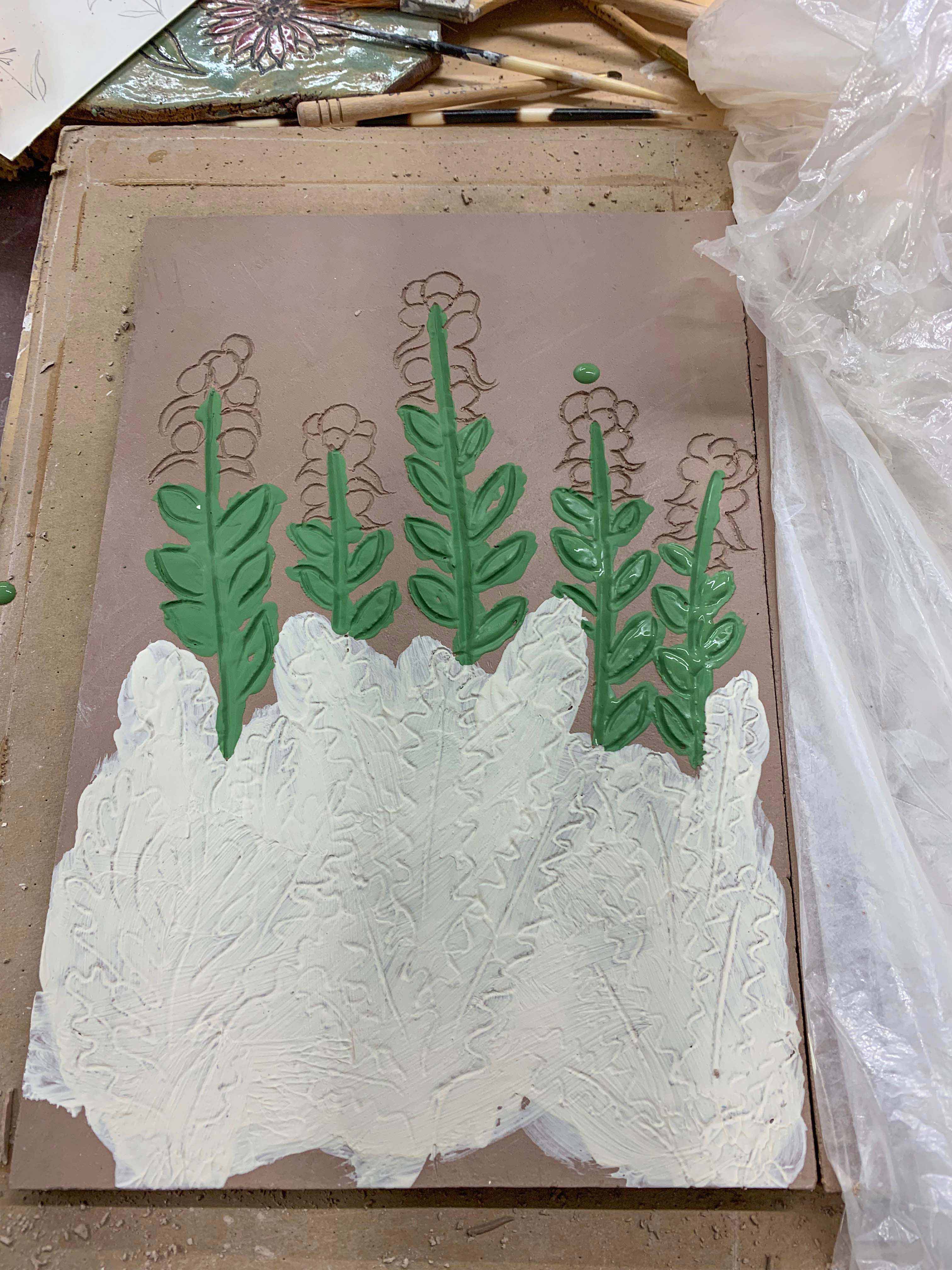
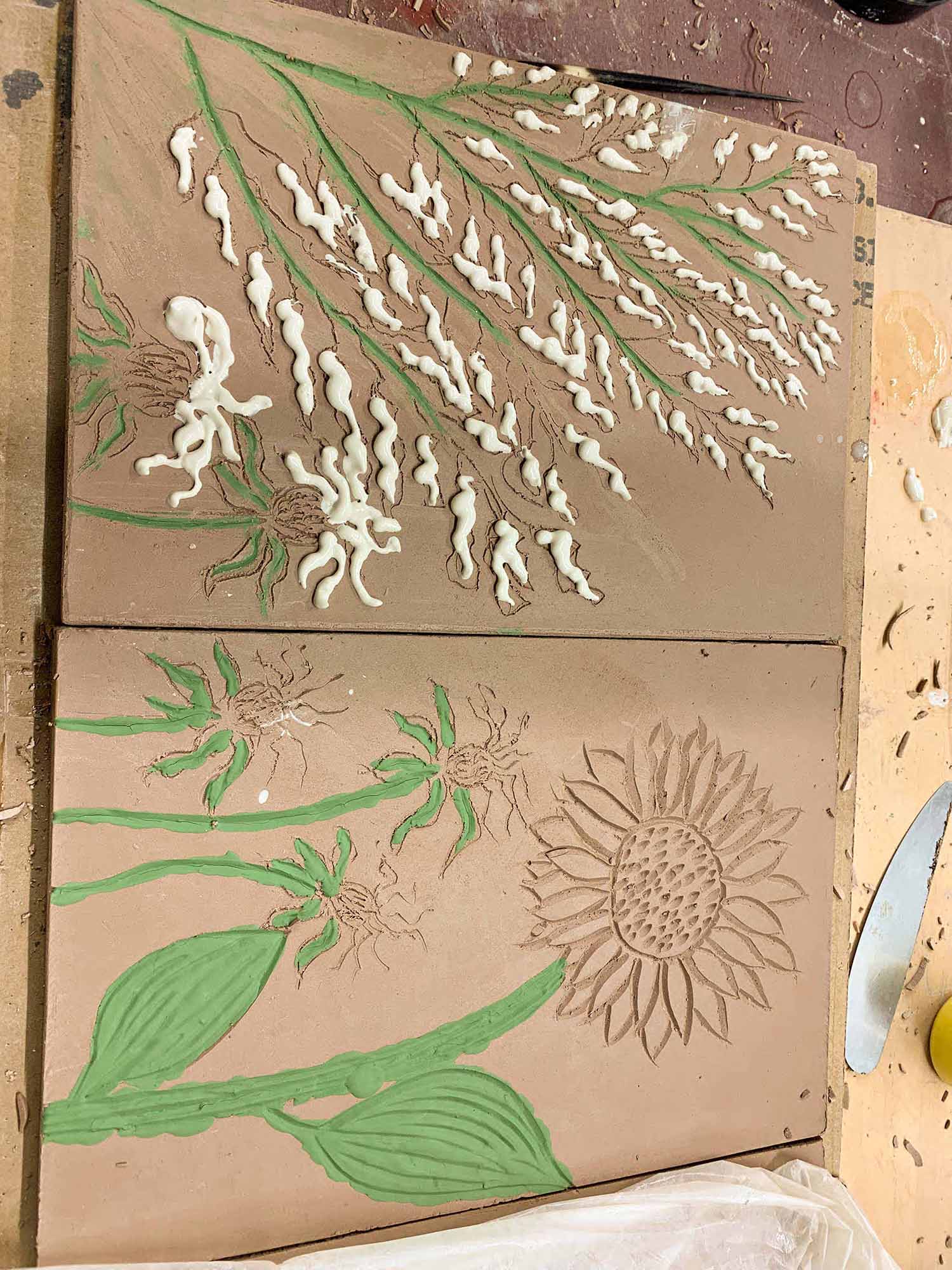
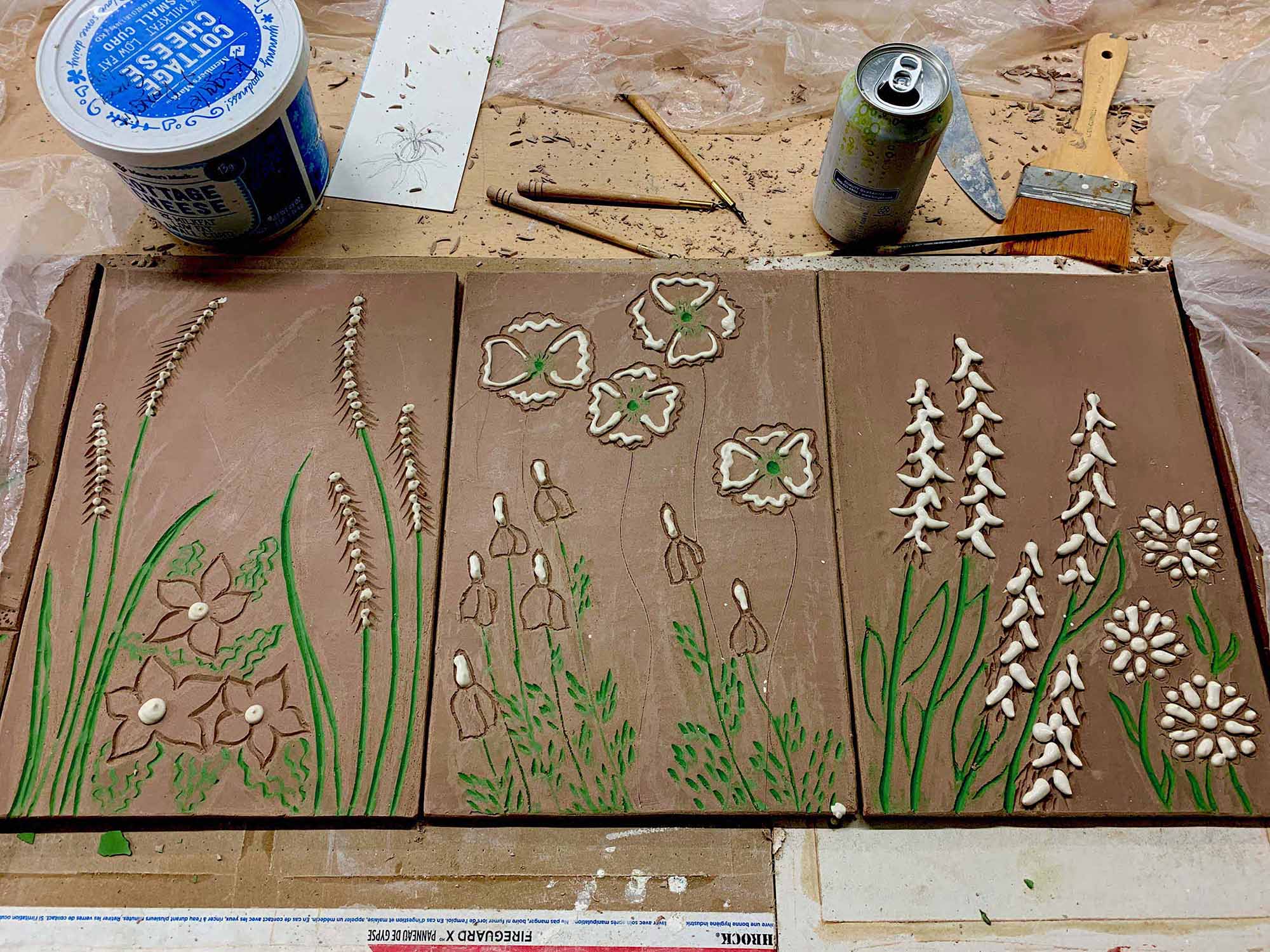
Once made and bisque, glazing and glaze firing followed.
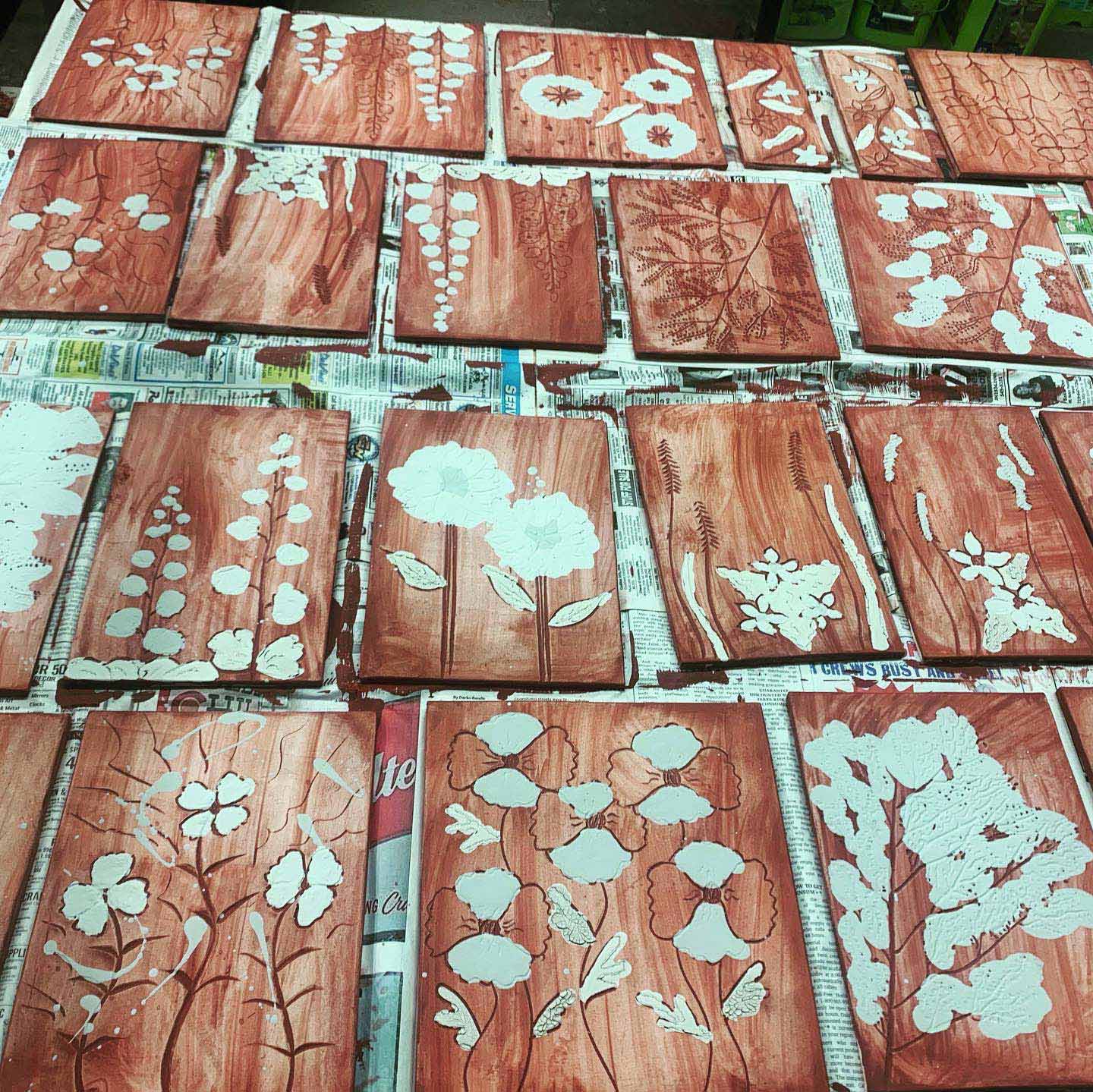
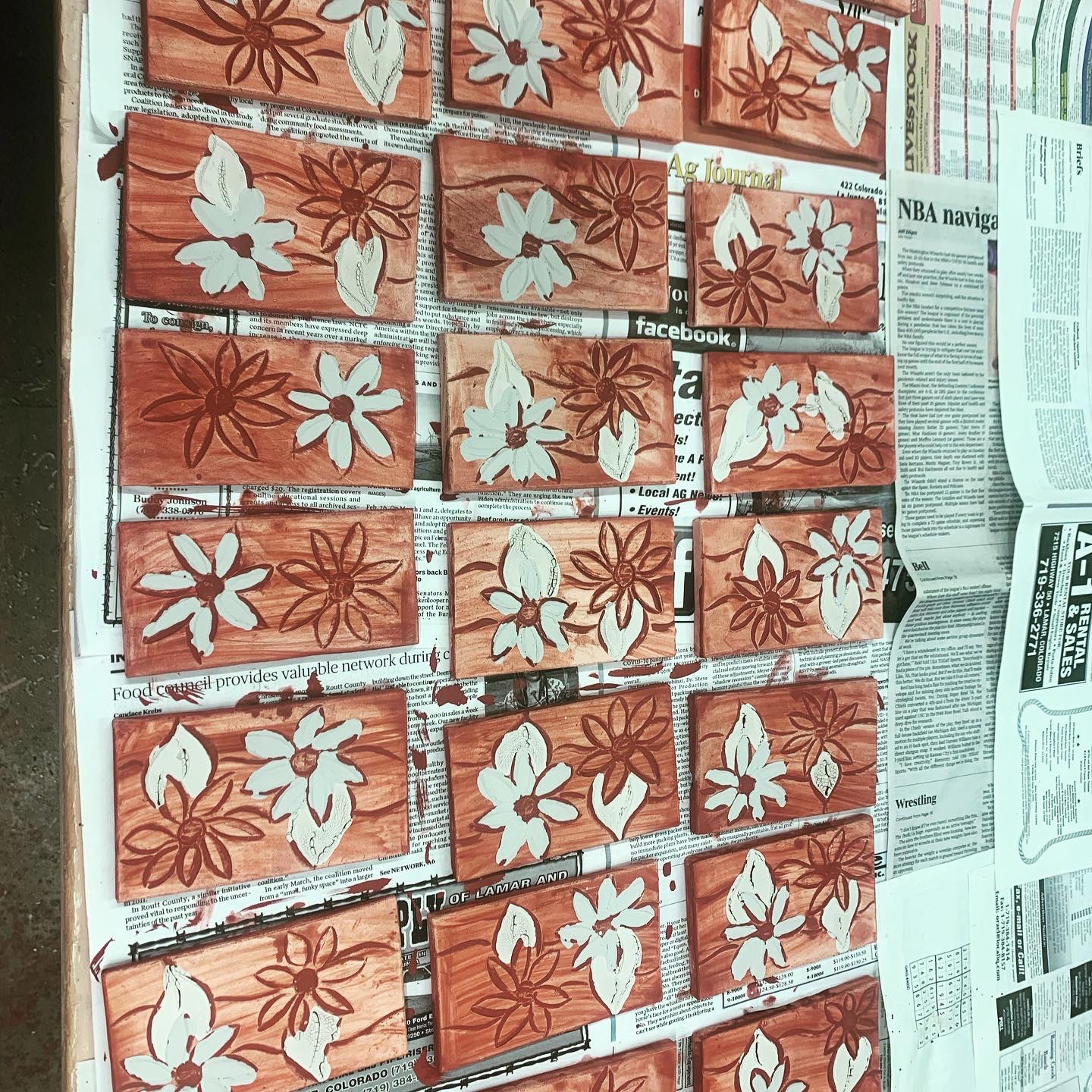
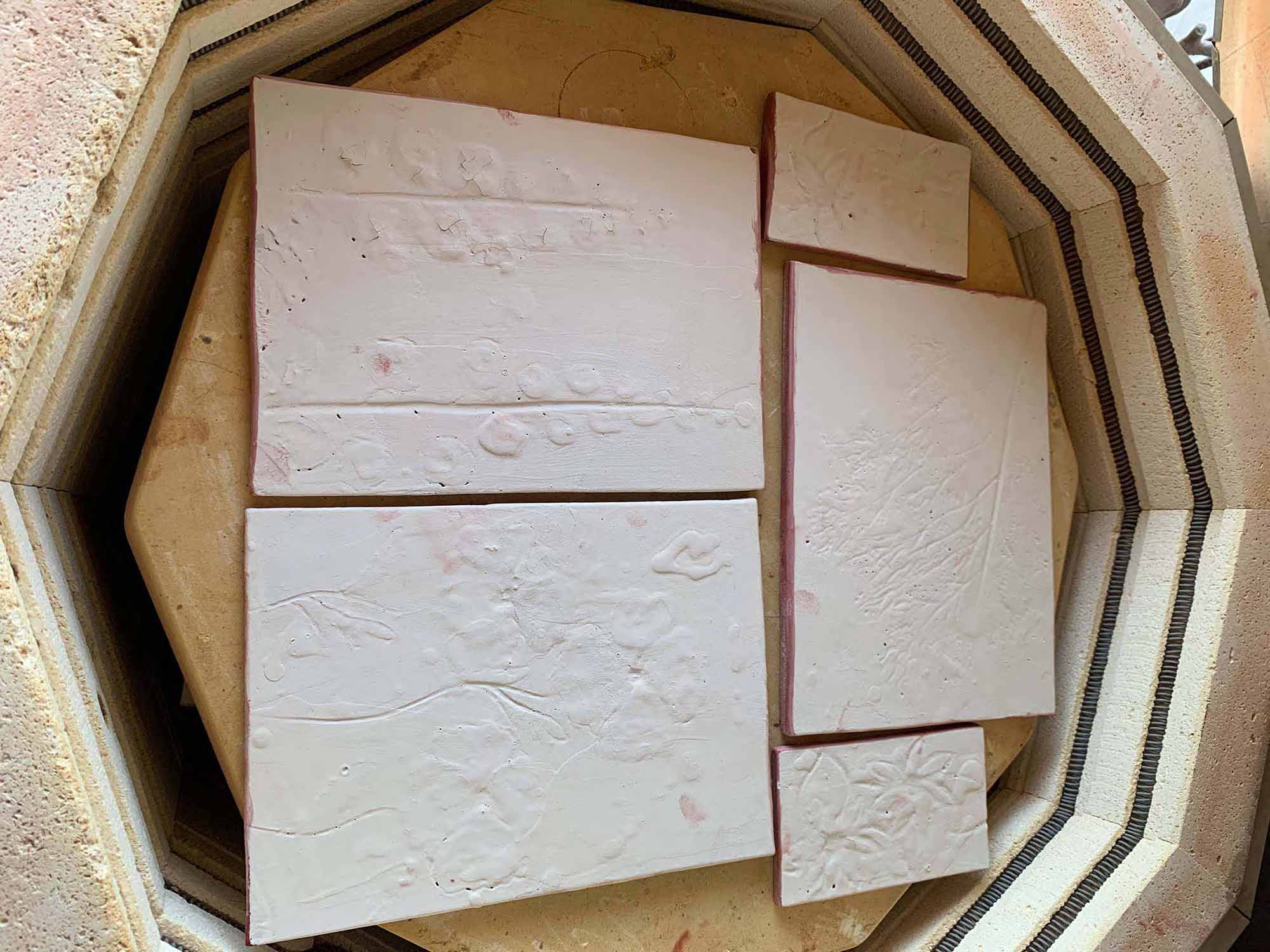
For all the fussy difficulty, the tiles fired beautifully
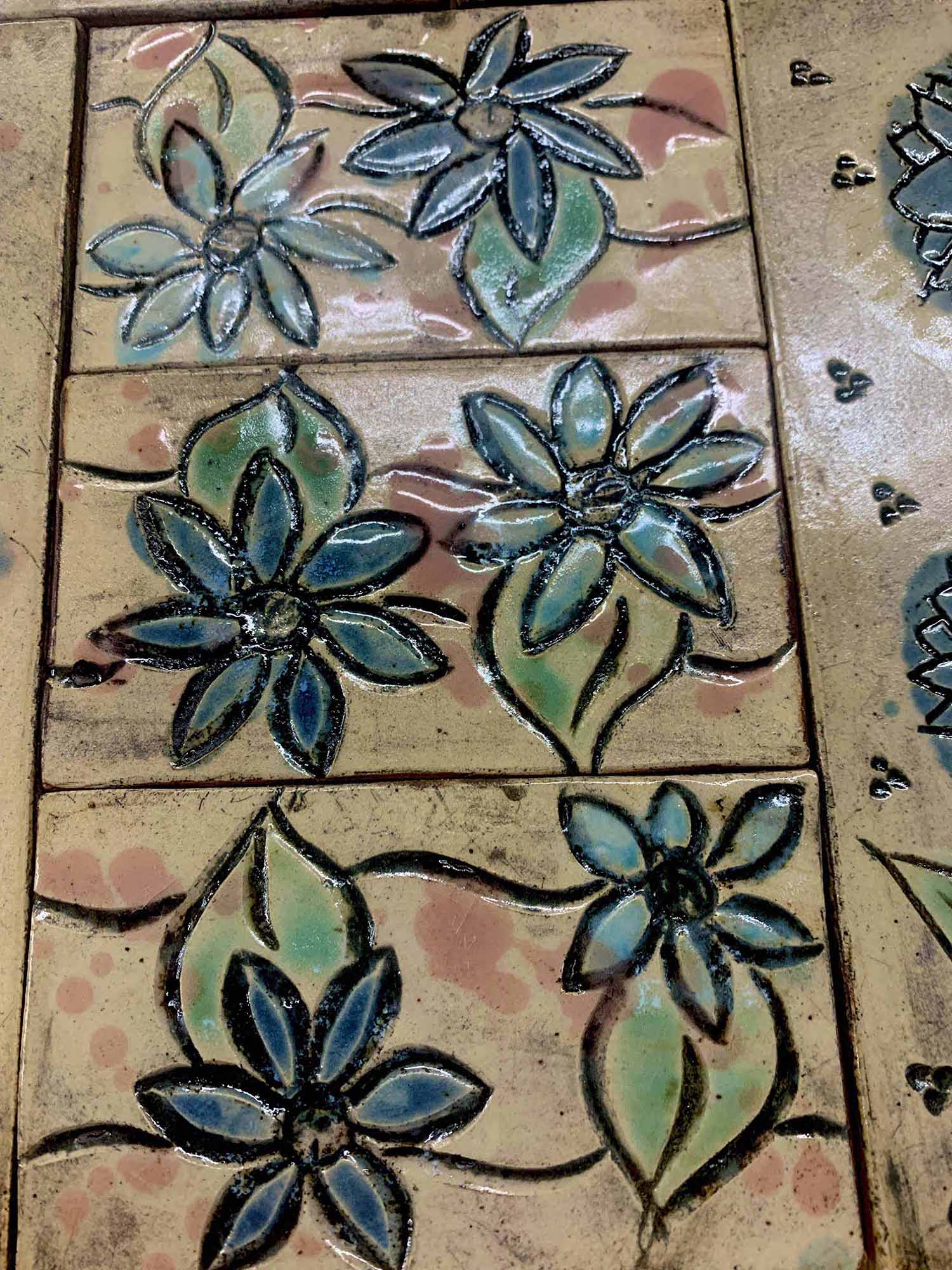
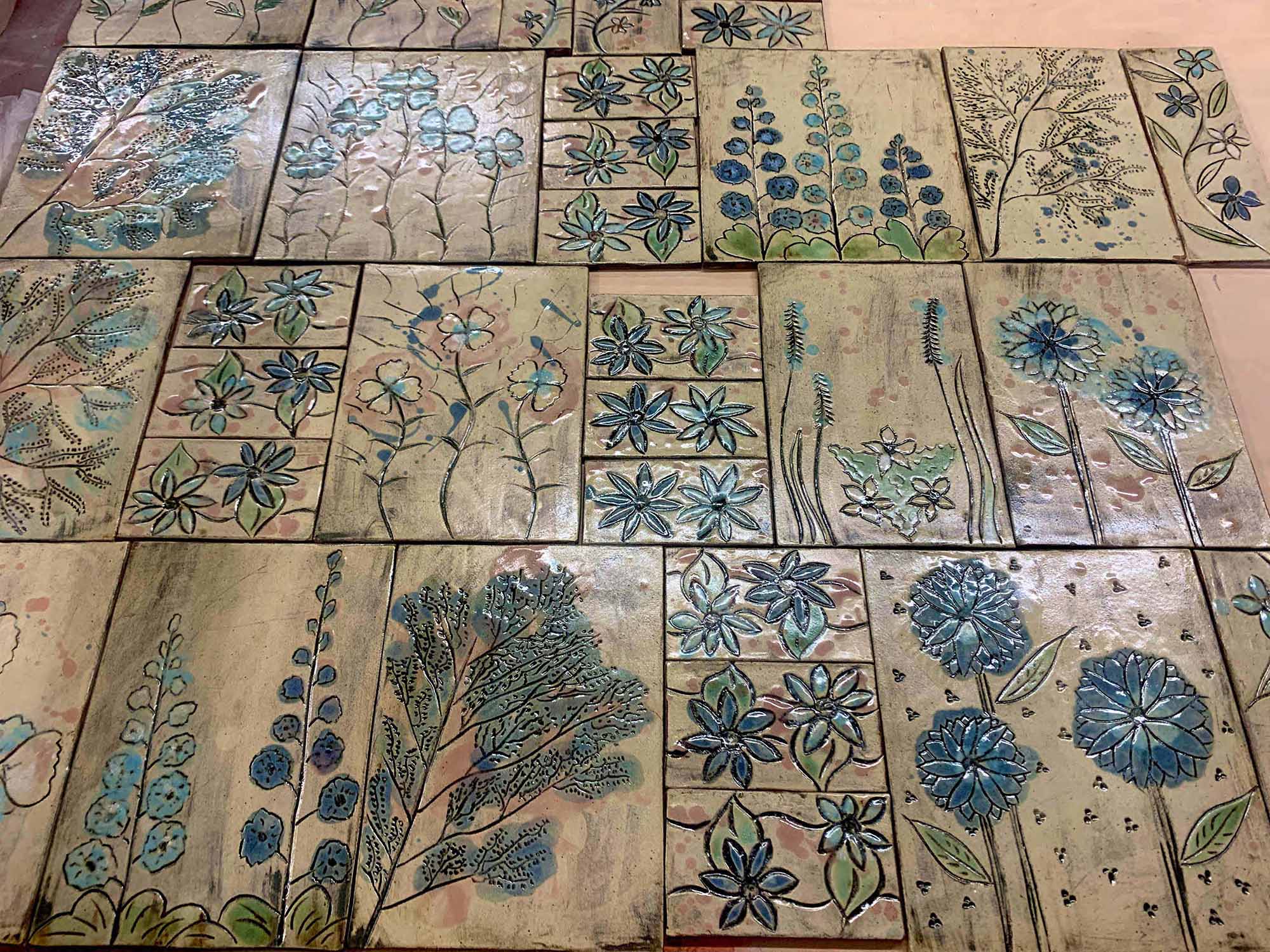
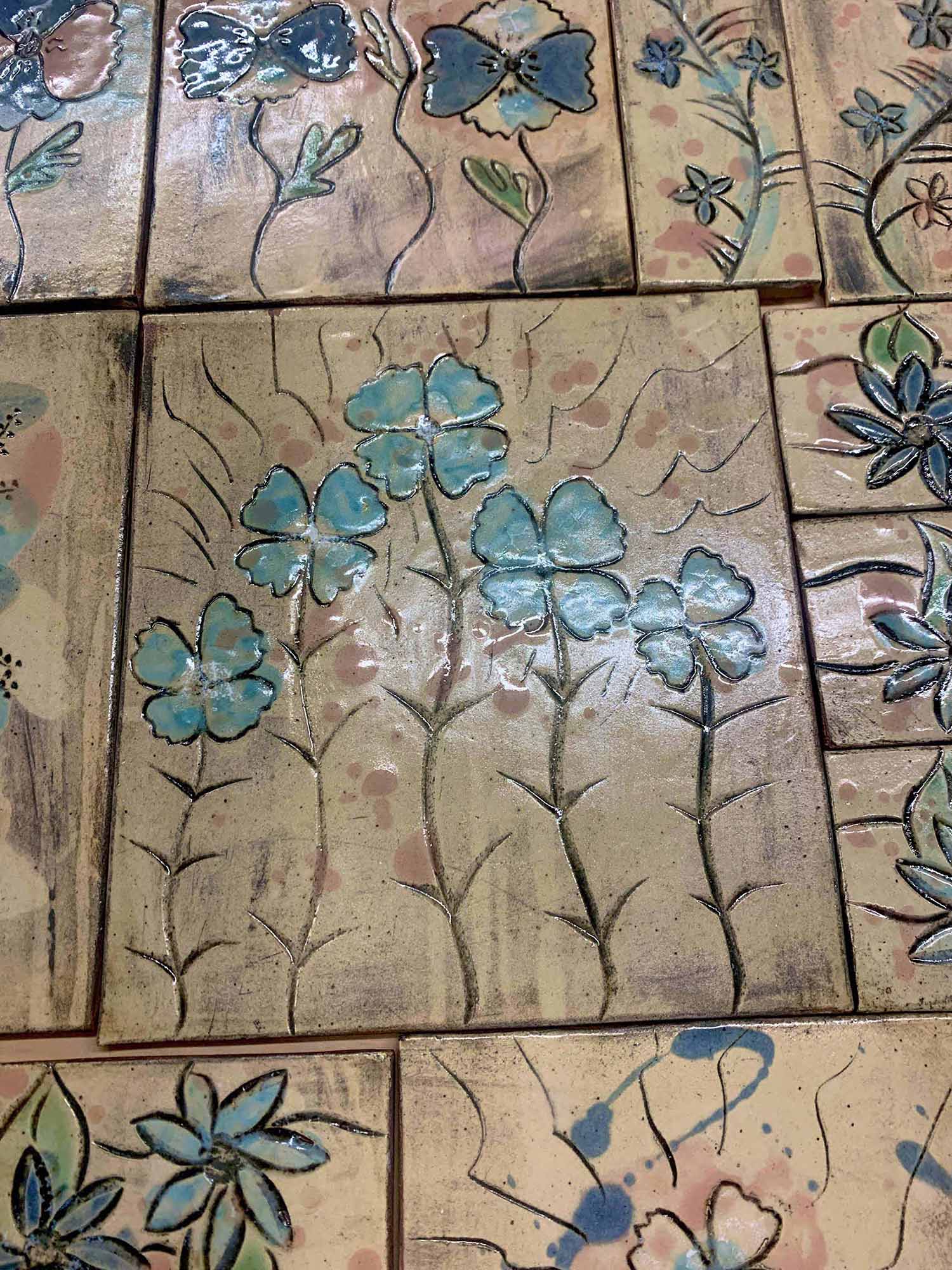
The most daunting part of any tile job is the installation. While I’ve trained for years in tile making, I’m a near novice at tile installation. Just like any new skill I’m trying to develop, I watched a lot of YouTube videos.
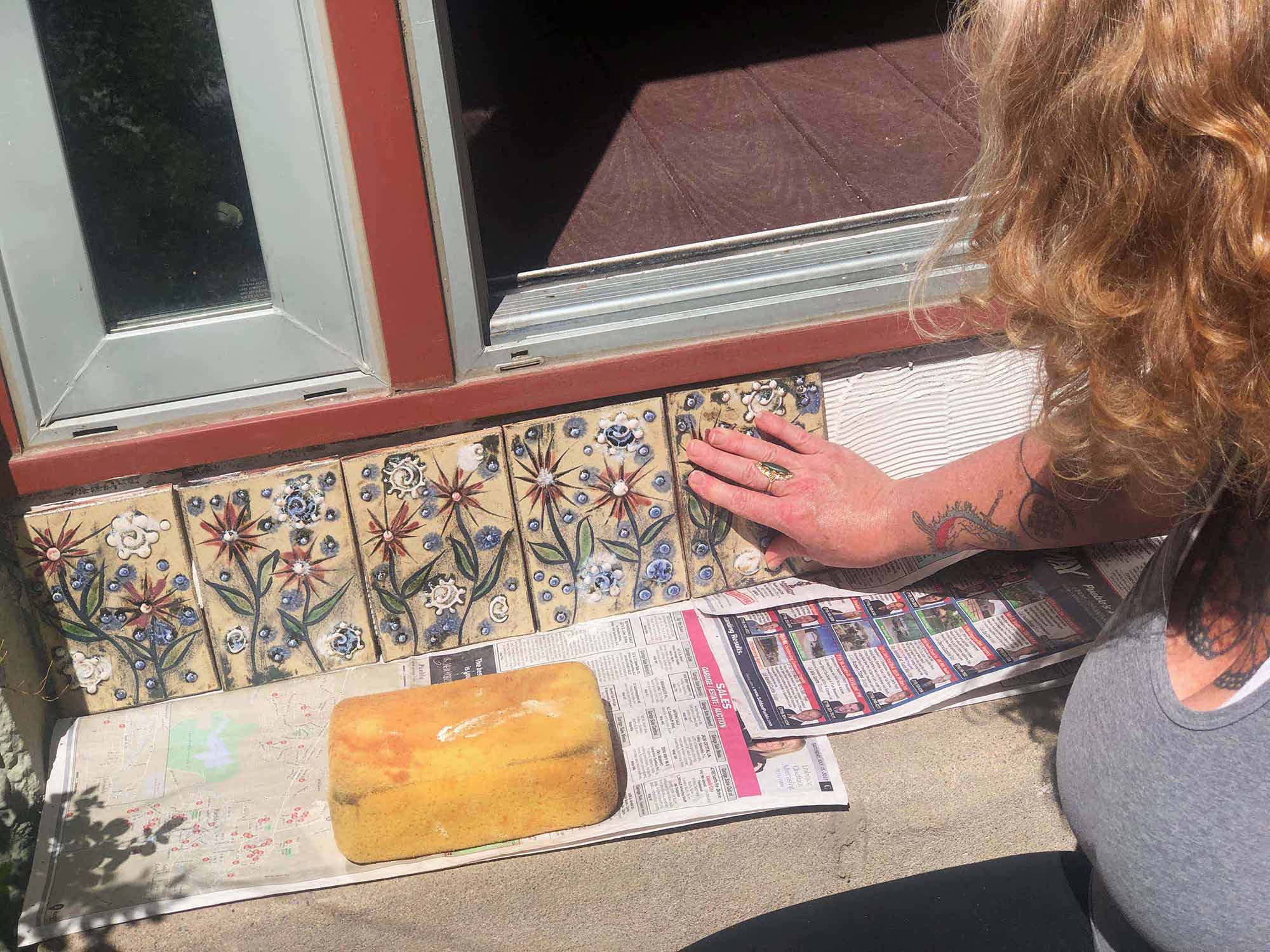

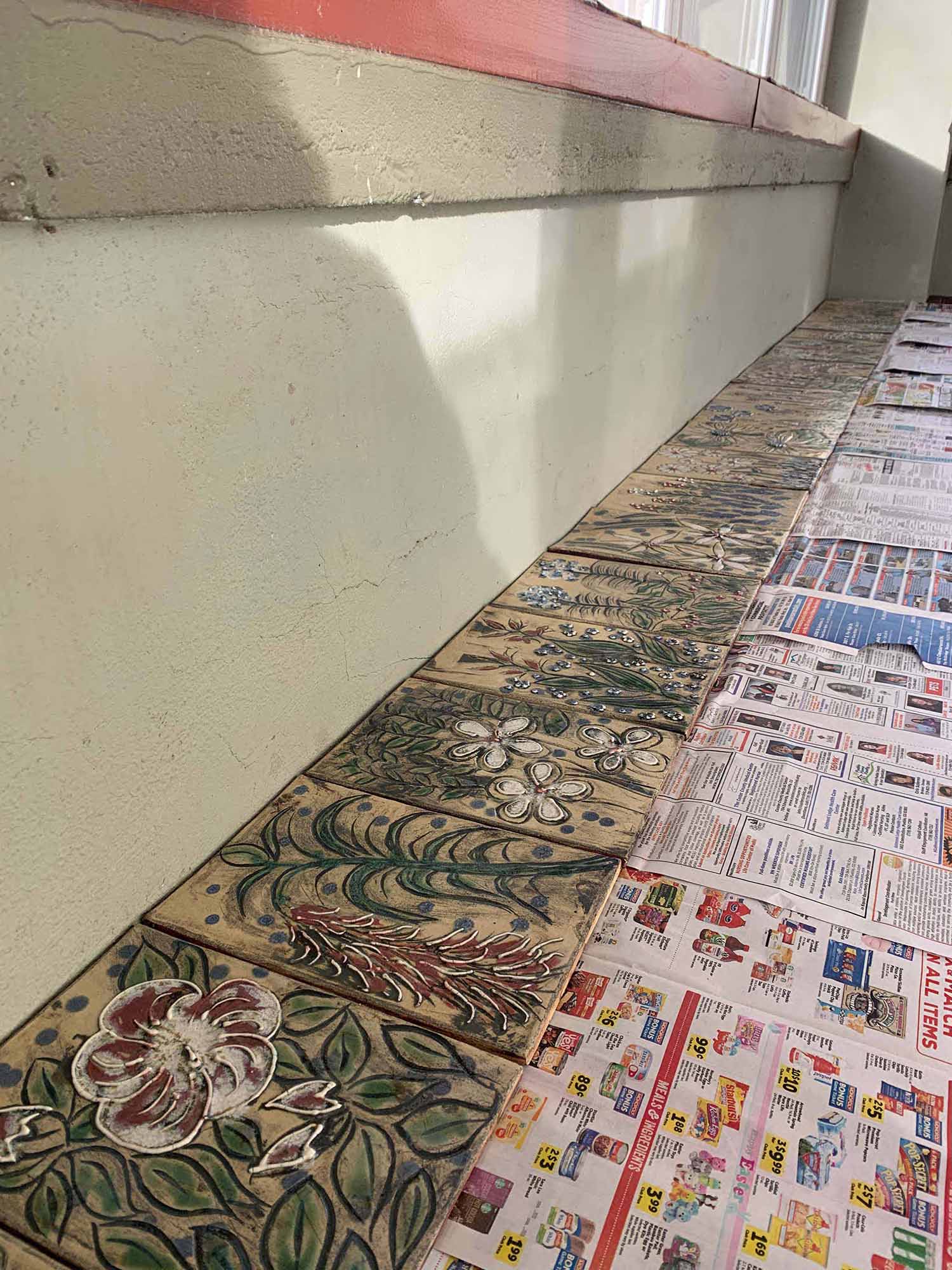
In the end I was thrilled with the piece, so grateful to have had the opportunity
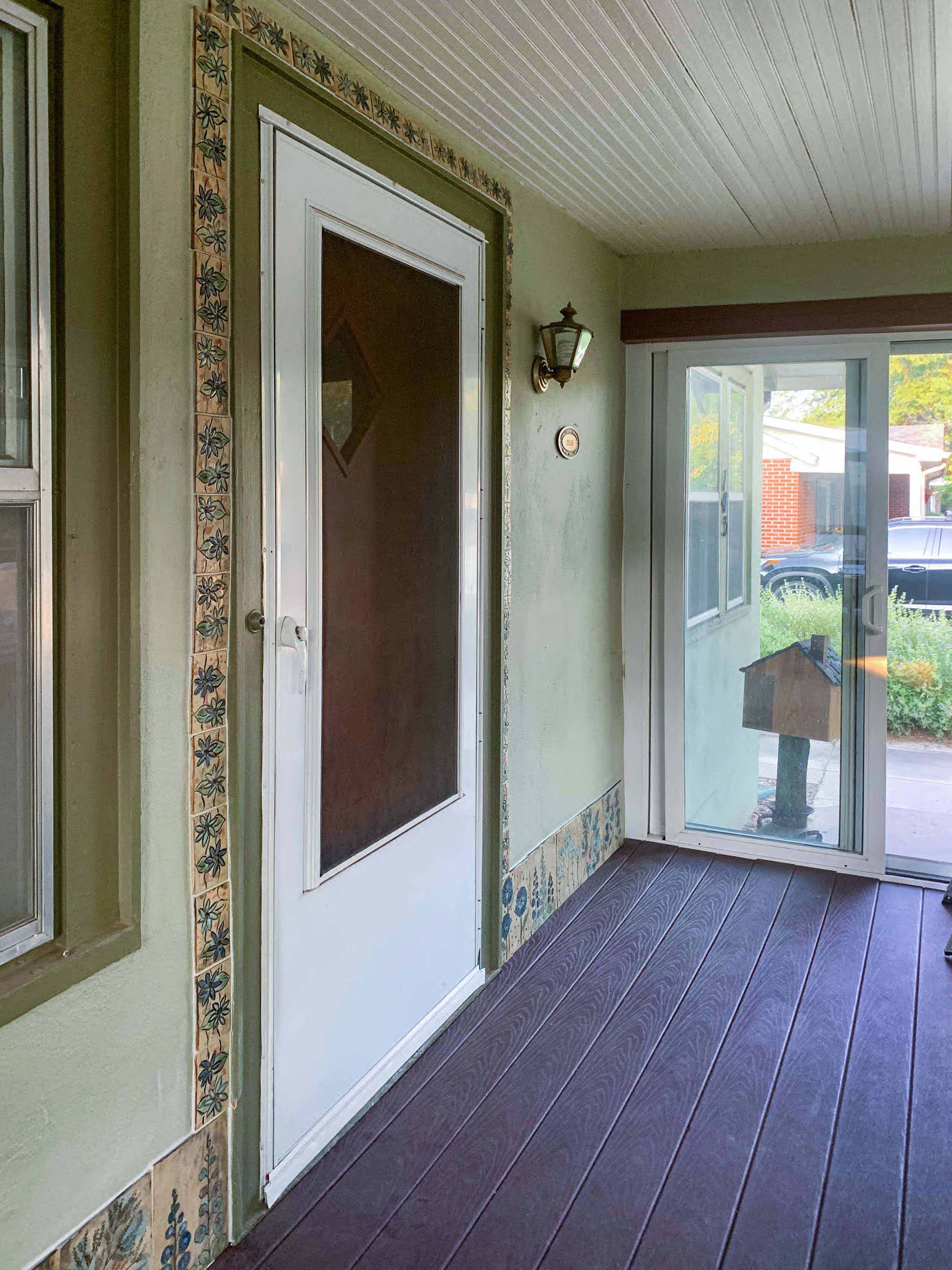
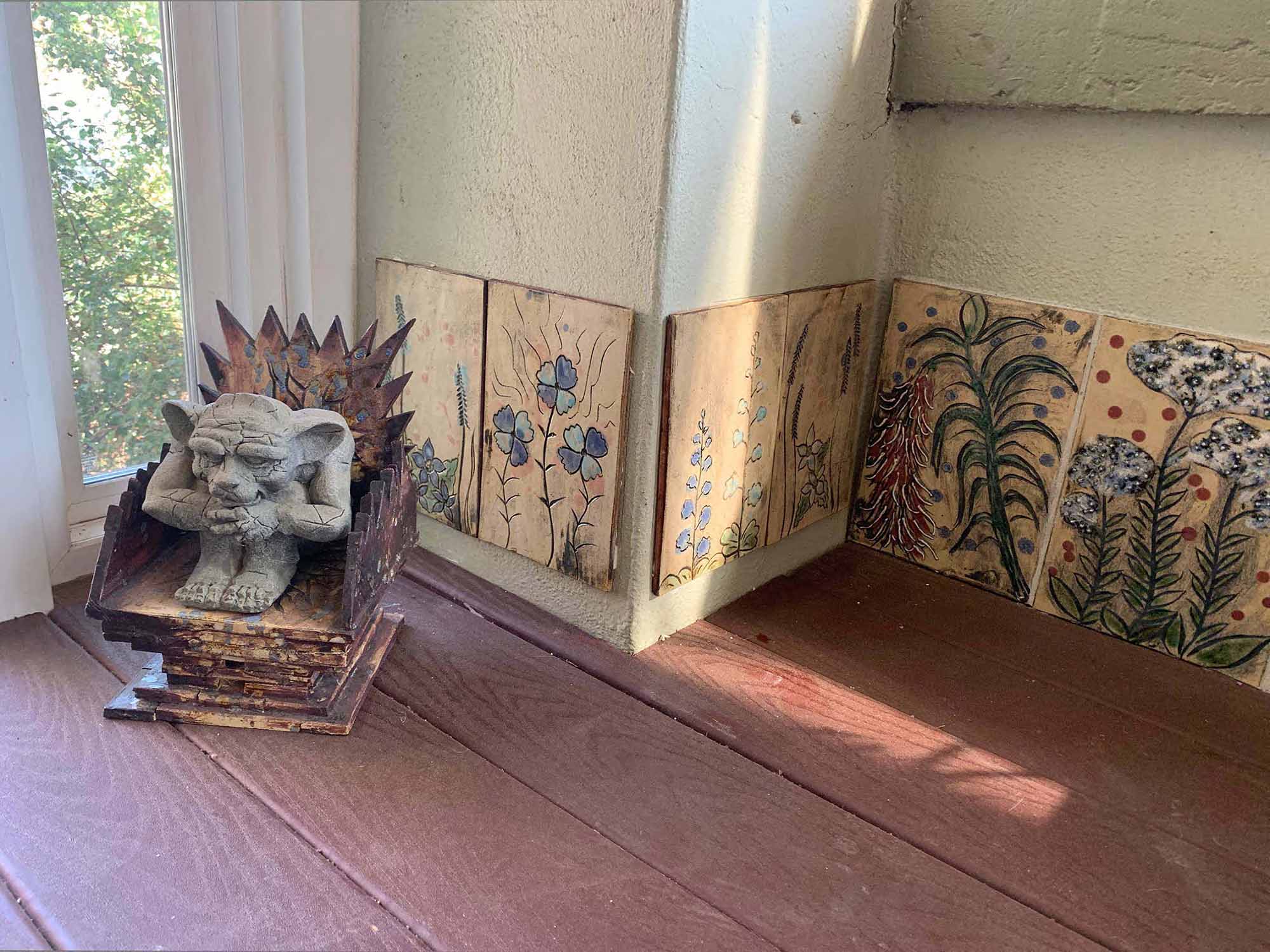